Manual Handling Of Goods: Nowadays, a lot of automated procedures are made to increase productivity at work. Even with these advancements, commodities still need to be handled by hand.

The definition of manual handling, the dangers associated with such duties, and how to begin implementing workplace safety measures to lower injuries and increase productivity are all covered in this article.
Manual Handling Defined
The phrase “manual handling” should go without saying. It describes any procedure, such as moving through a loading bay, where you must use your own body to maneuver around another object or person at work.
Given that the hazards of physical handling can also arise from repetitive strain that accumulates over time, the object being lifted or carried doesn’t have to be enormous or extremely heavy to be considered.
Processing occupations in warehouses and other logistics-related settings are particularly covered by this concept, which is applicable in a variety of professional contexts.
Identifying Risks In Your Work Environment
Manual Handling Of Goods You must first identify the dangers involved with manual handling before you can begin to reduce them. These will vary depending on the workplace.
It may be necessary to take into account repetitive strain injuries, occurrences involving objects falling off shelves, and stock damage in warehouses where workers must frequently pack up and shift stuff.
In smaller settings, like stores, you may still be at risk for back injuries from improper lifting techniques or in areas that are challenging to navigate, such stairwells.
Risk Reduction Possibilities
You can begin developing risk-reduction techniques as soon as you have a clear understanding of the hazards that exist in your particular setting.

Automate where possible
Using an automated solution from a business like Joloda Hydraroll can have a significant impact in settings like warehouses where a lot of manual handling takes place. Automation, for instance, can increase loading bay security.
Use the right equipment and tools
For awkward or heavy loads, use pallet jacks, trolleys, dollies, and hand trucks.
To reduce the need for physical handling, make sure there are hoists, conveyor belts, or forklifts among the lifting equipment.
To reduce the chance of trips or falls both before and after using tools and equipment, you can also encourage staff members to plan their route and avoid obstructions before lifting and transporting goods.
What Techniques Need To Be Taught?
When adhered to, certain procedures lessen the number of injuries caused by manual handling of products. For instance, comprehensive instruction and training on lifting methods are offered.

Lifting technique training
The worker must raise with their legs, not their back, in order to maintain good lifting posture. They lessen the load on their back muscles when they use their legs’ strong muscle groups.
Maintaining a straight back and keeping the weight close to the body are additional requirements for proper lifting posture.
Poor lifting posture and ignorance of one’s physical limitations can lead to injuries. Injuries can also result from lifting excessively large weights.
Manual Handling Of Goods recognizing the dangers of pushing and dragging big objects and correctly assessing the risks of manual handling jobs that require prolonged use.
Reminders and notifications about educational safety should also be posted in different places.
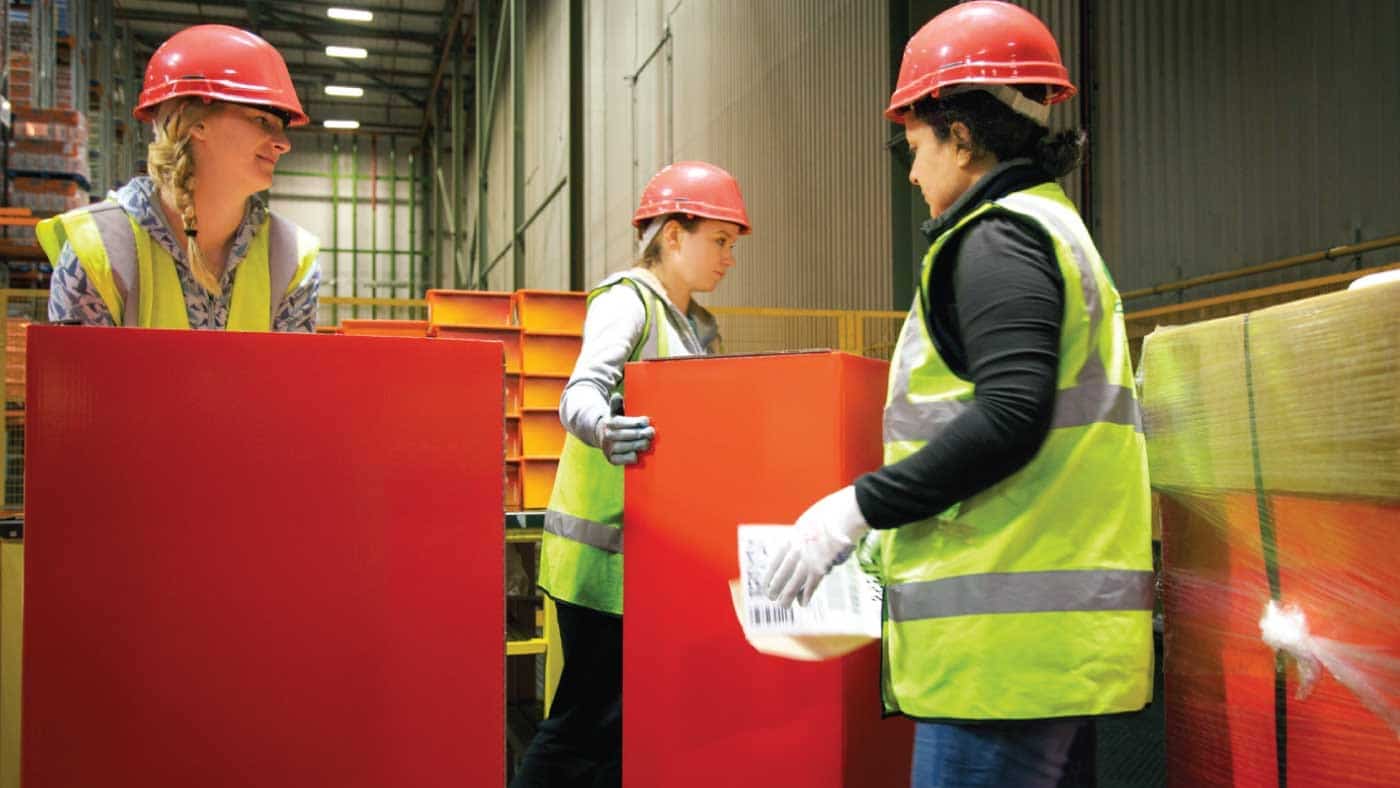
Stretching and Warm-Up
Implement initiatives that encourage workers to warm up and stretch before handling items in order to prevent muscle strain.
Make sure employees have breaks as well. Frequent breaks lessen fatigue, which is a major contributor to improper lifting technique and avoidable injuries.
Final Words
In most situations, no matter how much automation you do, some amount of manual handling will still be required. Nonetheless, a dedication to training, whether through seminars or e-learning courses that are incorporated into the onboarding procedure and updated frequently, helps reduce injuries.
To protect the health and safety of workers and guests in places like loading bays, businesses that need to handle items by hand must go by a number of safety laws and regulations.
Once more, the particular dangers related to the workplace will determine the type of training that needs to be conducted.
Although it is simple to ignore the risks associated with manual handling, these hazards are among the most serious and pervasive in today’s workplace.
The company gains from reduced expenses, fewer injuries, and less stock damage whenever manual handling safety is improved.